Industrial plants are under relentless pressure to deliver higher throughput, tighter tolerances, and richer traceability while containing costs. Forward-looking engineers have discovered that usb3 vision cameras and a modern machine vision camera portfolio can hit all three targets at once. By upgrading legacy GigE or analogue setups to USB3, plants unlock bandwidths approaching 350 MB/s, enabling fast, uncompressed transfers that suit today’s high-resolution CMOS sensors.
Beyond raw speed, usb3 vision cameras simplify deployment. Data, power, and trigger signals travel over a single off-the-shelf cable, shrinking control cabinets and shortening commissioning windows. That simplicity scales—whether you are installing a lone inspection station or a wall of cameras guarding every step of an SMT line. And because each vision device natively supports the GenICam protocol, the same software stack follows you from prototype to global rollout.
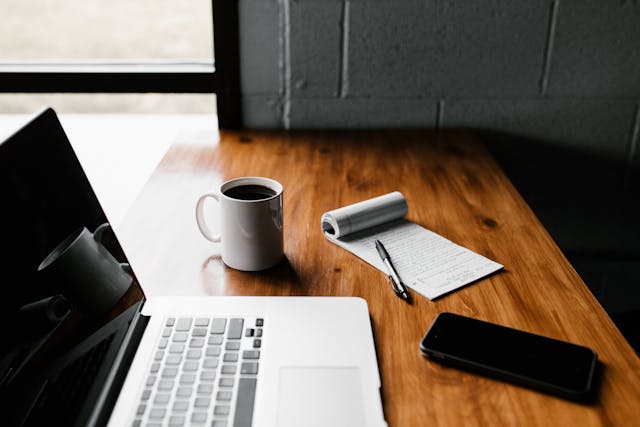
Post Contents
Benefit 1: higher throughput without sacrificing accuracy
USB3’s wide pipe lets an 8 MP sensor run north of 120 fps without the compression artifacts that plague older interfaces. One Tier-1 automotive supplier replaced four low-resolution units with a single next-gen module and recorded 38 % faster cycle times and a 12 ppm reduction in false rejects—proof that you don’t have to trade speed for precision.
Benefit 2: open standards lower integration risk
The USB3 Vision specification is stewarded by the A3 association, ensuring interoperability across vendors and generations. Whether you prefer a compact board-level module or a rugged IP67 housing, every compliant camera surfaces identical feature trees. That means fewer surprises during line expansions and faster recovery from supply-chain disruptions because a drop-in replacement really is just that.
Benefit 3: edge intelligence fuels predictive analytics
Many newer devices embed FPGA or SoC processing that handles debayering, glare suppression, or even neural-network inference in-camera. Offloading these tasks slashes host-CPU utilisation by up to 60 %, freeing cycles for MES communication or dashboard visualisation. When usb3 vision cameras stream metadata-rich frames directly into your data lake, quality teams shift from reactive scrap analysis to proactive process tuning powered by AI.
Benefit 4: effortless scalability for multi-camera and hybrid systems
A single industrial PC can host five USB3 units via a powered hub, making it economical to add colour, thermal, or 3-D triangulation views without ripping and replacing network infrastructure. This hub-and-spoke architecture also pairs neatly with containerised edge gateways, letting engineers drop additional machine vision camera nodes wherever new SKUs or regulations demand extra eyes.
Benefit 5: sustainability and long-term ROI
Energy efficiency rarely tops an automation wish list, but it should. USB3 devices operate at lower I/O voltages than Camera Link, cutting per-camera power draw by roughly 40 %. Across thousands of operating hours, that means measurable carbon-footprint gains and a quicker payback period. Falling sensor prices amplify the effect; the latest USB3 models often undercut equivalent GigE units by 15–20 %, making the upgrade business-case friendly even for small job shops.
Getting started: a roadmap for adoption
- Pick a high-impact pilot. Choose a contained process—solder-joint inspection, fill-level verification, or label OCR—and gather baseline metrics on takt time, defect counts, and rework hours.
- Quantify optical requirements. Work with a vision integrator to determine sensor size, lens F-number, illumination geometry, and depth-of-field. Proper photometrics prevent “garbage-in” data traps.
- Prototype with modular kits. Development bundles that include a USB3 camera module, cables, and reference software let you validate trigger logic and data rates in days, not months.
- Scale through standardisation. Document GenICam feature sets, driver revisions, and naming conventions so every future camera drops into the same golden image.
- Close the feedback loop. Feed annotated images to your analytics stack. Correlate defect trends with upstream parameters like temperature or spindle speed, and watch scrap curves bend downward.
The competitive edge you can’t postpone
Industry 4.0 is no longer a buzzword; it is a contract requirement from OEMs that expect digital proof of quality. Upgrading to usb3 vision cameras provides the pixels, performance, and protocol alignment that tomorrow’s market demands. By acting today, you future-proof your inspection architecture, empower your data scientists, and give every plant manager a clearer view of production health—literally and figuratively.
Ready to see more?
Whether you are retrofitting a single cell or designing a green-field smart factory, the path to sharper, faster vision starts with a single cable and the right camera. Make it a USB3-enabled one, and your production line will thank you for years to come.