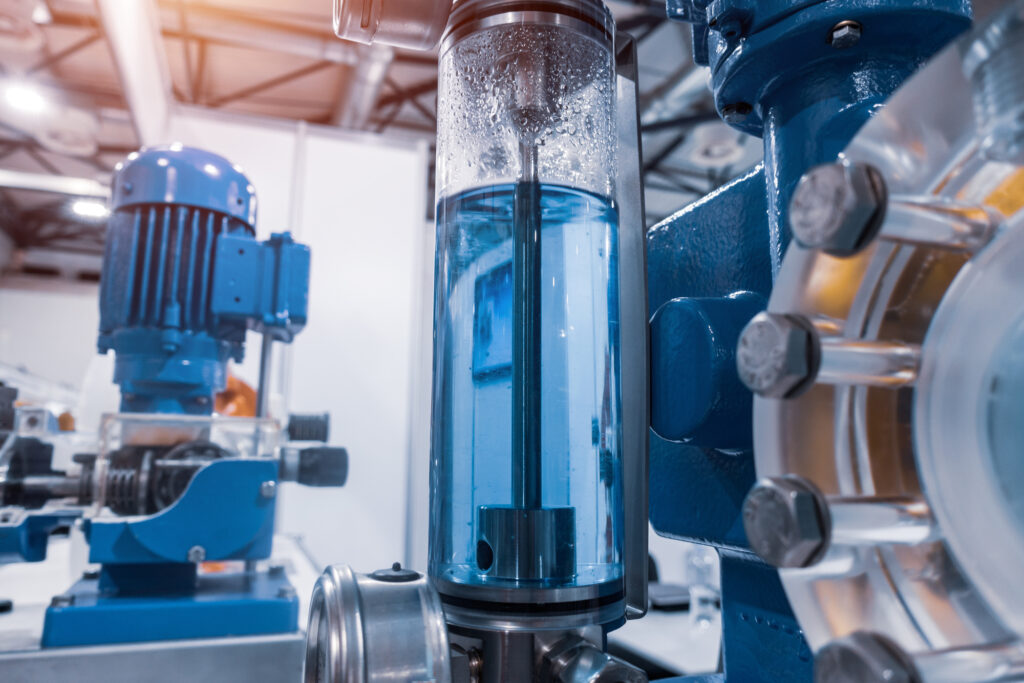
In the intricate world of scientific research and industrial processes, lab pump systems play a pivotal role that cannot be overstated. These sophisticated devices are designed to transport a variety of fluids—ranging from volatile chemicals to delicate biological samples—with precision and care.
That said, this guide aims to explore the complex world of lab pump systems, offering a deep dive into the various types available, their operating principles, and the diverse applications they serve. To learn more, visit knf.com/en/in.
Post Contents
The Significance Of Lab Pump Systems
The importance of lab pump systems extends across various fields, from pharmaceuticals and biotechnology to chemical engineering and environmental science. They are pivotal in tasks ranging from sample preparation, chemical synthesis, and chromatography to wastewater treatment and semiconductor manufacturing. The choice of a lab pump system is dictated by the specific needs of the operation, including the nature of the fluid (its chemical properties, temperature, and viscosity), the required precision in flow rate, and the need for sterility or avoidance of cross-contamination.
Types Of Lab Pump Systems
Understanding the different types of lab pump systems and their specific applications is crucial for selecting the right pump for your needs and ensuring efficiency, reliability, and safety in your operations. Here’s a look into the various lab pump systems and their applications:
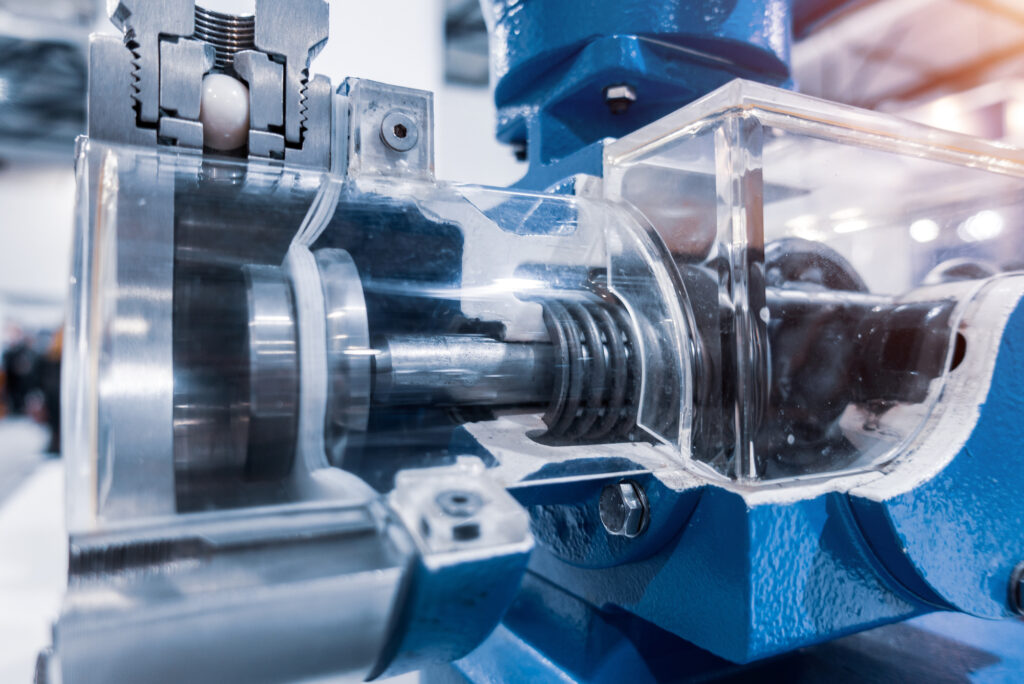
- Peristaltic Pumps
Peristaltic pumps operate on a simple yet effective principle, where a set of rollers mechanically compresses and releases a flexible tube, propelling the fluid contained within. This design ensures that the fluid never comes into direct contact with the pump mechanism, thereby maintaining purity and preventing contamination.
Moreover, these pumps are exceedingly versatile, given their ability to handle a wide range of fluids—from viscous slurries to sensitive biological samples. They are a staple in industries where sterility and contamination prevention are paramount, such as in pharmaceutical manufacturing for drug formulation, in food and beverage production for processing ingredients, and in clinical settings for administering intravenous therapies.
- Centrifugal Pumps
Centrifugal pumps leverage the kinetic energy of a rotating impeller to move fluids. As the impeller spins, it imparts velocity to the fluid, converting this velocity to pressure as the fluid exits the pump.
This type of pump excels in applications requiring the movement of large volumes of fluid with relatively low viscosity, making it a popular choice in sectors like water treatment, where it’s used for pumping clean water, and in biofuel production, where it assists in the processing of various biofuels.
Furthermore, centrifugal pumps equipped with artificial intelligence (AI) algorithms can optimize performance in real-time, adjusting to changes in demand or operating conditions. AI can also predict wear and tear on impellers and seals, scheduling maintenance before failures occur.
- Diaphragm Pumps
Diaphragm pumps, known for their reliability and versatility, use a reciprocating diaphragm to create a vacuum or pressure that moves fluid through the pump. This type of pump can handle a wide variety of fluids, including those highly viscous or containing solid particles, without risk of damage or wear to the pump internals.
Their ability to pump aggressive chemicals safely and efficiently makes them particularly valuable in laboratories and industrial settings where chemical resistance is a critical concern. From chemical processing plants to hazardous waste management, diaphragm pumps provide a secure solution for transferring corrosive, abrasive, and potentially hazardous fluids.
- Gear Pumps
Gear pumps are characterized by their simplicity and effectiveness, using the meshing of gears to pump fluid. As the gears rotate, they create a void that draws fluid into the pump, transporting it around the exterior of the gears to the outlet where it is discharged.
This mechanism allows for the smooth handling of high-viscosity fluids, such as syrups in the food industry, polymers in chemical manufacturing, and resins in plastic production. Their precision and efficiency in delivering a constant flow rate make gear pumps an indispensable tool in applications requiring exact dosing or consistent fluid handling.
- Piston Pumps
Piston pumps employ a reciprocating piston within a cylinder to generate high-pressure fluid flow. This design allows them to operate effectively under a wide range of conditions, delivering fluids at high pressures with precise control overflow rates.
Their robustness and reliability make them particularly suited for applications that demand high performance, such as in high-pressure liquid chromatography (HPLC) systems used in analytical laboratories for separating, identifying, and quantifying compounds within a mixture. In the oil and gas industry, piston pumps are utilized for high-pressure chemical injection and hydrocarbon transfer, underscoring their versatility and capability in challenging environments.
- Vacuum Pumps
Vacuum pumps are essential in applications requiring the removal of air and other gases from a sealed volume to create a vacuum. These pumps come in various types, including rotary vane, diaphragm, and turbomolecular pumps, each designed to achieve different levels of vacuum and suited to specific applications.
In the laboratory, vacuum pumps are crucial for processes like freeze-drying, where they remove moisture from samples without damaging their structure, and in mass spectrometry, where they create the necessary vacuum for analyzing chemical compounds. The semiconductor and electronics manufacturing industries rely on vacuum pumps for processes requiring highly controlled environments, highlighting their importance across a broad spectrum of scientific and industrial fields.
Conclusion
The advancement of lab pump technologies promises to elevate their utility, enhance efficiency and enable further innovation in numerous sectors. This article has sought to underscore the significance of lab pump systems, highlighting their essential contribution to the advancement of scientific research and industrial processes.